
Precision casting plays a critical role in aerospace and defense. It ensures components meet exact specifications, which is essential for safety-critical applications. Industries rely on this process to create durable parts from high-performance alloys like titanium. With a market value of $16.3 billion in 2023, precision casting suppliers continue driving innovation and reliability.
Key Takeaways
- Precision casting ensures safety and reliability by producing components with exact specifications, crucial for aerospace and defense applications.
- The process allows for the creation of lightweight, durable parts from high-performance alloys, enhancing fuel efficiency and reducing maintenance needs.
- By minimizing waste and utilizing eco-friendly practices, precision casting supports sustainability goals while maintaining high-quality standards.
Understanding Precision Casting
What is Precision Casting?
I often describe precision casting as a manufacturing process that delivers unmatched accuracy. It creates components with precise dimensions and smooth surface finishes, far superior to traditional methods like sand casting. This process ensures that parts meet exact specifications, which is critical in industries like aerospace and defense. Even the smallest deviation can lead to failure in these fields. Precision casting allows us to produce high-performance components that comply with strict industry standards.
Key Features of the Process
The precision casting process involves several detailed steps. Each step ensures the final product meets the required quality. Here’s how it works:
- MOLD DESIGN
- WAX INJECTION
- ASSEMBLY TREE
- SHELL MAKING
- DEWAX
- CASTING
- KNOCKOUT
- CUT OFF
- GRINDING
- INSPECTION AND POST TREATMENT
- FINISHED CASTINGS
This step-by-step approach allows us to create complex geometries and innovative designs. It also supports the use of high-performance materials, making it ideal for aerospace and defense applications.
Role of a Precision Casting Supplier in Quality Assurance
A precision casting supplier plays a vital role in ensuring quality. They use advanced tools like micrometers, CMM machines, and vision systems to maintain precise tolerances. I’ve seen how process control software monitors raw materials, chemical analysis, and temperature during production. This ensures every stage is optimized for reliability. By partnering with a trusted supplier, industries can achieve the high standards required for safety-critical applications.
Benefits of Precision Casting for Aerospace and Defense
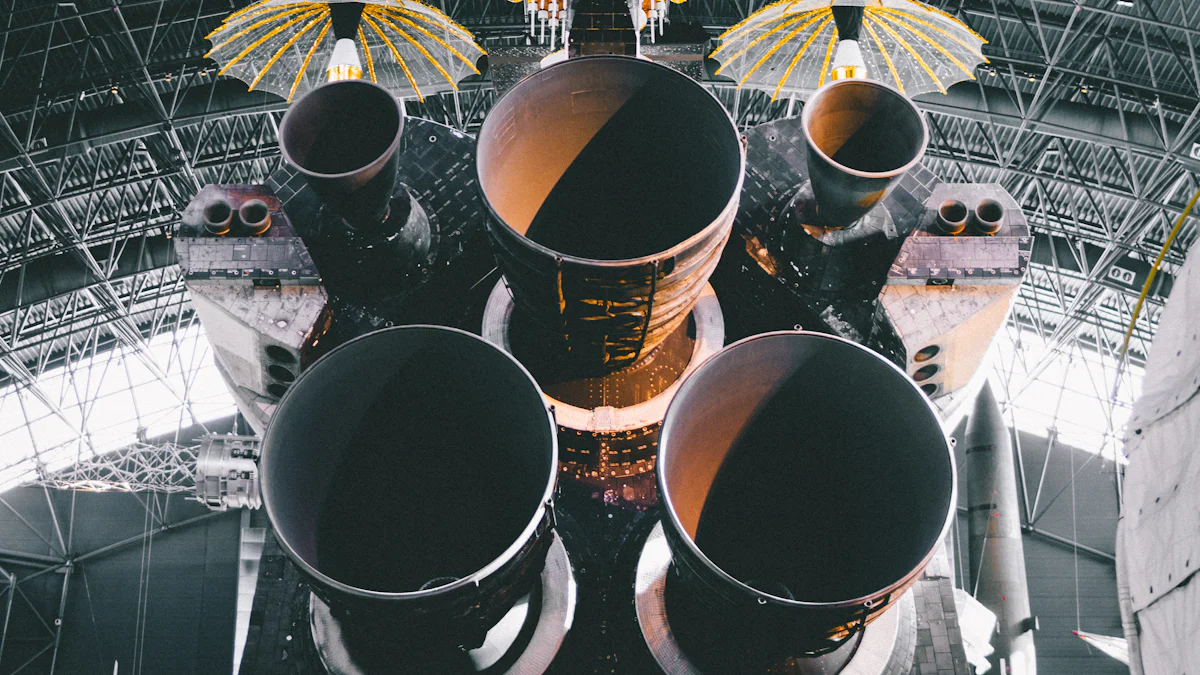
Tight Tolerances for Safety-Critical Applications
I’ve seen how tight tolerances make a huge difference in aerospace and defense. They ensure components perform reliably under extreme conditions. Here’s why they matter:
- Safety improves because parts won’t fail during critical operations.
- Performance gets a boost since precise dimensions enhance aerodynamics and fuel efficiency.
- Interchangeability allows parts from different locations to fit perfectly, simplifying maintenance.
- Reliability increases as components behave predictably, reducing risks.
- Regulation compliance becomes easier, avoiding penalties and ensuring legal operation.
Precision casting achieves these tolerances, making it a trusted choice for safety-critical applications.
Material Versatility for Extreme Conditions
The materials used in precision casting handle the toughest environments. I’ve worked with alloys like nickel and cobalt, which resist high temperatures and corrosion. Some of the most common materials include:
- 400 Series Stainless Steel for strength and wear resistance.
- Cobalt Alloys for gas turbines and aerospace parts.
- Nickel Alloys for extreme heat and corrosive settings.
- Inconel Alloys for jet engines and industrial furnaces.
This versatility ensures components perform well, even in the harshest conditions.
Complex Geometries for Advanced Designs
Precision casting allows engineers to create intricate designs that traditional methods can’t match. I’ve seen how it produces lightweight parts with hollow structures and internal channels. This process supports advanced geometries like curved or multi-layered designs, which improve performance in aerospace systems. The smooth finishes and tight tolerances make these complex shapes possible without sacrificing strength or durability.
Durability and Weight Reduction for Enhanced Performance
Durability and weight reduction are critical in aerospace and defense. Precision casting excels in both areas. It creates lightweight components with thin walls and hollow structures, reducing aircraft weight and improving fuel efficiency. At the same time, it uses high-performance alloys like titanium to ensure parts withstand extreme conditions. Durable components also require fewer repairs, saving time and resources.
Sustainability and Cost-Effectiveness in Manufacturing
Precision casting supports sustainability by minimizing waste. I’ve noticed how it uses only the necessary amount of metal, reducing material costs. Reusable molds and recyclable leftovers further enhance its eco-friendliness. The process also creates near-net-shape components, cutting down on machining and saving energy. This efficiency lowers production costs while maintaining high-quality standards, making it a cost-effective solution for industries.
Applications of Precision Casting in Aerospace and Defense
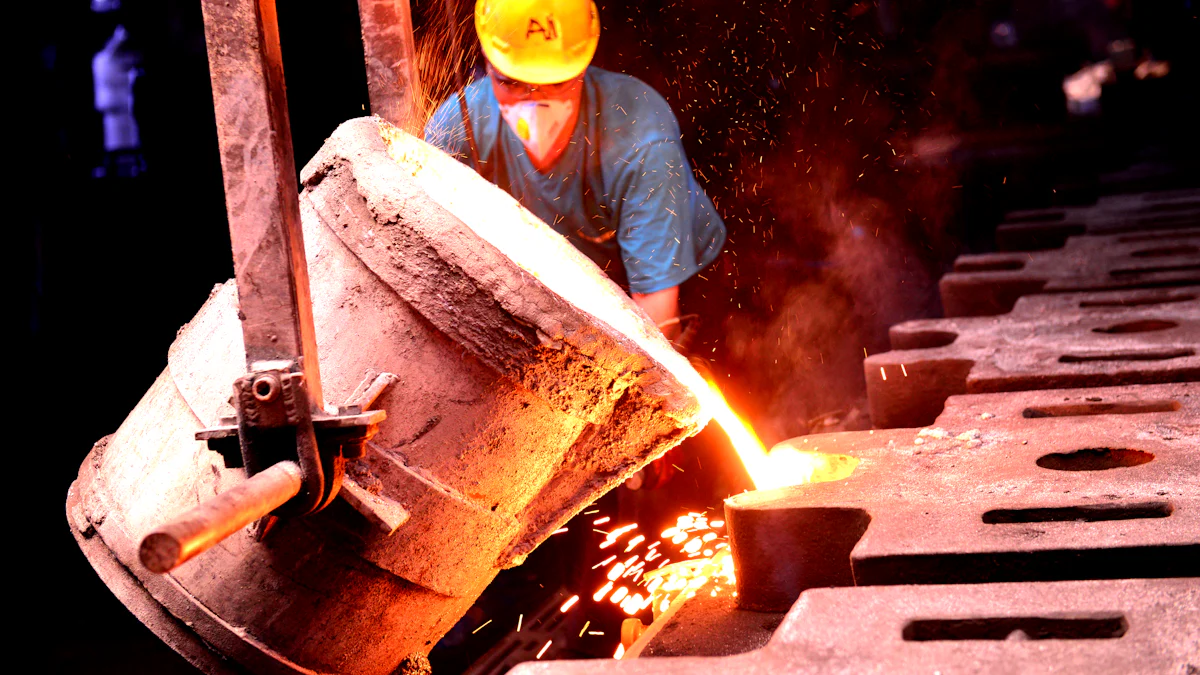
Aerospace Components: Turbine Blades, Engine Parts, and Structural Elements
I’ve seen how precision casting transforms aerospace manufacturing. It produces critical components like turbine blades, engine parts, and structural elements with unmatched accuracy. These parts must meet strict requirements for safety and performance. For example:
- Nozzle assemblies, often made from superalloys, withstand extreme heat in jet engines.
- Valve mounts and manifolds ensure smooth operation in fuel and hydraulic systems.
- Mounting brackets and flanges provide structural support while reducing weight.
Precision casting also creates parts for cabin controls, environmental systems, and landing gear. This versatility makes it indispensable for aerospace applications.
Defense Equipment: Weapon Systems, Armor, and Specialized Tools
In defense, precision casting ensures reliability under extreme conditions. I’ve worked with components that require tolerances as tight as ±0.005 inches. This level of precision is vital for weapon systems, where even minor deviations can compromise performance. The process also handles complex designs, such as undercuts and intricate slots, which are common in military technology.
Precision casting minimizes surface defects and internal porosities, reducing the need for additional machining. This saves time and enhances reliability. By creating single, monolithic components, it eliminates weak points, ensuring durability in critical applications like armor and specialized tools.
Innovations and Future Trends in Precision Casting
The future of precision casting excites me. Advances in technology, like combining casting with 3D printing, are revolutionizing the industry. This hybrid approach allows for even more intricate designs and faster production. High-performance alloys, such as titanium and 7000 series aluminum, are becoming standard. These materials reduce weight while maintaining strength, aligning with aerospace goals.
Sustainability is another trend shaping the industry. Precision casting minimizes waste and supports eco-friendly practices. As industries demand lightweight, durable, and cost-effective solutions, precision casting will remain at the forefront of innovation.
Precision casting plays a crucial role in aerospace and defense. I’ve seen how it ensures safety and reliability by delivering components with exact specifications. This process meets strict standards, producing durable parts that perform under extreme conditions.
- It creates high-performance alloys that resist heat and pressure.
- It achieves tight tolerances for safety-critical applications.
- It minimizes waste, supporting sustainability goals.
As these industries evolve, precision casting will continue driving innovation. It enables complex designs, reduces maintenance needs, and supports greener aviation. I believe its unmatched accuracy and adaptability make it indispensable for future advancements.
FAQ
What makes precision casting better than other manufacturing methods?
I’ve found precision casting delivers tighter tolerances, smoother finishes, and supports complex designs. It also reduces waste and works with high-performance materials for extreme conditions.
Can precision casting handle lightweight aerospace components?
Yes! I’ve seen it create lightweight parts with thin walls and hollow structures. This reduces aircraft weight while maintaining strength and durability.
How does precision casting contribute to sustainability?
Precision casting minimizes waste by using only necessary materials. Reusable molds and recyclable leftovers make it an eco-friendly choice for aerospace and defense industries.
Send your message to us:
Post time: Jan-02-2025